1. This machine line is designed for manufacturing elevator cable sheath with material such as PVC , TPU (specified by client).
2. Suitable for manufacturing sheath with multiple core insulation in parallel structure , such as H05VVH6-F , H05VVD3H6-F etc . E.g.
Model | HH-E-120 |
Inlet Wire | 1-3mm |
Finished Wire | Max. Width 80/100, be specified |
Extrusion Material | PVC, TPU, etc. |
Dia. of Screw | 120mm |
Max Output | 280KG/H |
Max Line Speed | 50-140 M/Min |
Inlet quantity | Max.12 or be specified |
Electric environment | 380V±10% , 50Hz±3% (assisting AC 220V , DC 24V) |
Machine dimension | L45000mm*W6000mm*H5000mm |
2. Machine Component
No. | Description | Quantity |
1 | Dual-head motorized pay-off device | 1 set |
2 | Dual -head Magnetic powder tension pay-off | 1 set |
3 | Wire straightening unit - 5 roll | 1 set |
4 | Oil applying unit | 1 set |
5 | 120 main extruder | 1 set |
6 | Self-centering head specially designed | 1 set |
7 | Automatic drying and feeding machine | 1 set |
8 | Electric control box | 1 set |
9 | Fixed water tank | 1 set |
10 | Diameter gauge | 1 set |
11 | Caterpillar tractor | 1 set |
12 | High pressure air dryer | 1 set |
13 | Meter counter | 1 set |
14 | Spark tester | 1 set |
15 |
Gantry take-up |
1 set |
3. Accessories of 120 Elevator Cable Extrusion Machine
- Dies
- Extruder head
- American blower
- Dry suction machine
- Spool
- Heating ring
4. Function Features
- High Efficiency: Capable of extrusion speeds ranging from 50 to 140 meters per minute, ensuring rapid production cycles.
- Precision Control: Incorporates a diameter gauge and self-centering head for maintaining stringent dimensional accuracy.
- Robust Construction: Built with durable materials and components, including a 120mm screw diameter and high-pressure air dryer, to ensure long-lasting performance.
5. Ease of Operation
- User-Friendly Interface: Features an electric control box with intuitive controls for easy operation.
- Automatic Functions: Equipped with an automatic drying and feeding machine to streamline the extrusion process.
- Maintenance: Designed for easy access and maintenance, reducing downtime and operational costs.
6. Application Fields
- Elevator Industry: Ideal for manufacturing elevator cables with high-quality sheaths.
- Electrical Industry: Suitable for producing various types of cables requiring robust and reliable sheaths.
7. Advantages Comparison
- Superior Extrusion Capacity: With a capacity of 280kg/h, it outperforms many other machines in its class.
- Flexibility: Capable of handling a wide range of wire diameters and sheath widths, offering versatility for various production needs.
- Precision: Advanced control features ensure precise production, reducing waste and increasing product quality.
8. Quality Assurance
- High Standards: Manufactured with premium materials like nitrided treated cylinders and stainless steel components for enhanced durability and performance.
- Reliability: Designed to meet rigorous industry standards, ensuring consistent and reliable operation.
9. Customer Support and Service
- Comprehensive Support: Offers robust customer service, including technical support, maintenance, and training.
- Customization: Ability to customize machine parameters and components to meet specific client requirements.
10.On-spot Meeting


11.Trial Before Shipment
https://www.youtube.com/watch?v=vT1aXfV1sh8
https://www.youtube.com/watch?v=1e5z7DOoWYg
12. Frequently Asked Questions (FAQs)

1. Plastic scorching Plastic scorching is a common quality defect in the plastic extrusion process, and its attention is shown as follows: the temperature is too high; there is a lot of smoke, strong irritating smell, and cracking sound in the die mouth of the machine head; There are coke particles in the layer; there are continuous bubbles at the glue joint;
The main reasons are:
1) The temperature control is super high to reach the plastic thermal degradation temperature;
2) The screw has not been cleaned for a long time, and the accumulated scorch material is extruded with the molten plastic;
3) The heating or shutdown time is too long, so that the plastic in the barrel is decomposed by heat for a long time;
4) The temperature control instrument is out of control or inaccurate, resulting in high temperature decomposition;
5) The cooling system of the extruder is not turned on, causing the material to be overheated by shear friction. Therefore, during the extrusion process, it is necessary to check whether the heating and cooling systems are working properly; the extrusion temperature should be set according to the process requirements and the speed of the screw; reasonably control the heating time, and regularly clean the extrusion system.
2. Poor plasticization of the extrudate As mentioned above in the temperature control requirements, the plasticization problem has been mentioned. Generally, the poor plasticization is mainly manifested as: the extruded cladding has a toad skin; the plastic surface is black, dull, and has Small cracks; the extrusion layer has obvious seams at the glue; the main reasons are:
1) The temperature control is too low, especially the nose part;
2) Other plastic particles of different properties are mixed in the insulating or sheathing material;
3) The screw is turned too fast, and the plastic is not completely plasticized;
4) The plastic itself has quality problems. In view of the above reasons, attention should be paid to the rationality of extrusion temperature control; the quality and product name of the materials used should be confirmed; the extrusion speed should not be increased blindly by pursuing output; strengthening the storage of raw materials, especially in the plastic drying process; To enhance extrusion pressure and screw return.
3. There are pores or bubbles in the section of the extruded cladding. The main reasons are:
1) The temperature control is too high (especially the feeding section);
2) There is moisture in the plastic when it is damp;
3) Parking for a long time, the decomposed plastic is not cleaned up;
4) The natural environment has high humidity;
5) The content of water or vapor in the cable core is too high. For the above reasons, the temperature of each section of the screw should be reasonably controlled; the materials used should be pre-dried in advance; the process operation requirements should be strictly controlled to improve the ability to judge the degree of plasticization of plastics; attention should be paid to the production environment and material storage and storage conditions.
4. The size of the extrusion package is unqualified, which is mainly manifested as eccentricity; the thickness or outer diameter of the sheath is out of tolerance; the main causes are: unstable extrusion and traction speed;
1) The outer diameter of the cable core changes too much;
2) The extrusion temperature is too high, resulting in a reduction in the amount of extrusion;
3) Too much impurities in the plastic block the filter to reduce the flow of plastic;
4) The tension of the take-up and pay-off line is unstable;
5) The core selection is too large (extrusion type) or the length of the core wire bearing area is too short and the core is eccentric;
6) Improper selection of die spacing;
7) The temperature of the extruder head is uneven;
8) The concentricity of the extrusion die is not adjusted;
9) The temperature of the feed port is too high, which makes feeding difficult and affects the material flow;
5. The adhesive strength of the longitudinal wrapping tape is unqualified. The main reasons are:
1) The temperature of the extrudate is too low;
2) Excessive overflow of ointment filling;
3) The production line speed is too fast, so that the sheath is rapidly cooled;
4) The temperature of the hot water tank is too low, and it is close to the die;
5) The drawing ratio of the mold matching is too small, or the mold matching is unreasonable, so that it forms a loose bag;
6) The melting point of the longitudinally wrapped composite film is too high; according to the above reasons, attention should be paid to the mold matching requirements, and if necessary, it should be adjusted according to the cable core; the sheath should not be rapidly cooled to improve the bonding ability; Excessively reduce the temperature of the machine head; pay attention to the filling amount of the ointment, it is better to scrape a thin layer of the cable core with your fingers.
6. The appearance of the extrusion package is unqualified, and the unqualified appearance of the extrusion package is mainly manifested as scratches on the surface of the extrusion package; roughness with trachoma or microcracks; any defects caused by insufficient plasticization. The main reasons are:
1) The selection of extrusion die sleeve is unreasonable. Too small will cause hemp pattern; too large will cause disjoint or squeeze loose;
2) There are impurities in the extrusion die sleeve, which are stuck and scratched on the surface of the sheath.
3) The heating temperature of the extruder head is too high to cause roughness, or the temperature is too low to cause micro-cracks;
4) There is damage in the sizing area of the die sleeve;
5) The sheath is scratched in the sink;
1. Full machine customization
2. Machinery installation layout design
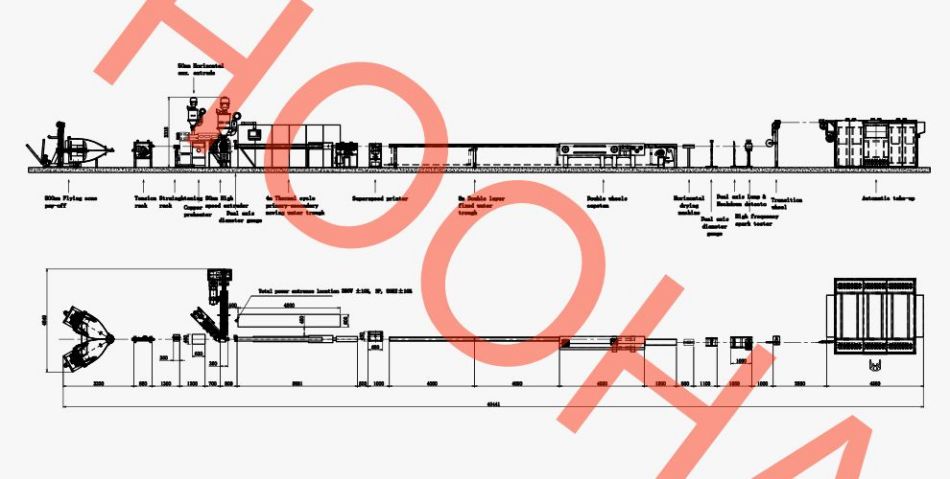
3. On-spot installation service (negotiable)
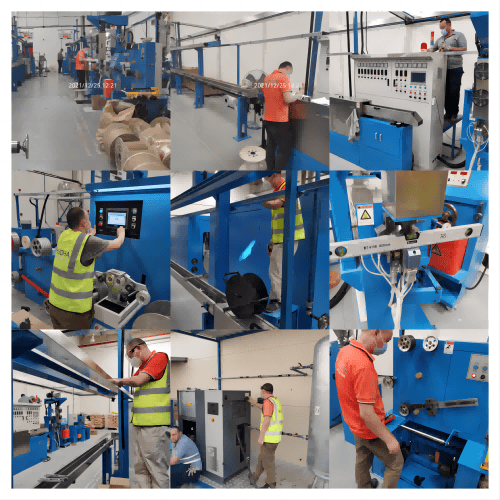
4. Whole factory layout design

5. Accessories supply
Tips and dies | Heating plate | Bobbins and reels |
![]() |
![]() |
![]() |
6.Hooha Service
Pre-sale
1.Experienced engineer team provides customized solutions and equipment layout drawing service
2.Professional engineer team provides overseas face-to-face service to offer advice and solution
3.Advanced trading system guarantees high-efficient communication
4.High-performance team including experienced salesmen,order supervisors, shipping managers, finance managers,wire and cable engineers would give you more detailed and accurate consultation service
Mid-sale
1.Professional follow-up system ensures high-quality service including live production video shooting,etc
2.Quality control system with professional engineers ensures project goes smoothly
3.Quality checking service with a test report before delivery ensures products quality
After-sale
1.Overseas on-site installation guidance and technical support including previous testing, operation instruction and talent training
2. Free lifetime online consultation service
3. Long-time maintenance, reconstruction and upgrade services of the wire and cable equipment
4. Additional service support, such as raw material or accessories supply and suggestions, etc.
7. 24-hours consulting team

8.Certificates and Exhibitions
