Upward continuous casting oxygen-free copper rod production line (called the plant as follow), it is used for producing the big length shining/bright oxygen-free copper rod, the big length shining oxygen-free copper tube pellet and the big length shining oxygen-free copper flat pellet, etc.
No. | Items | Feature |
1 | annual output | 2 000 tons ( annually uninterrupted ) |
2 | strands quantity | 4 strands |
3 | pulling pitch | 1-5mm adjustable |
4 | pulling speed | 0~3.2 m/min |
5 | take-up machine | 1 set |
6 | rod diameter | Φ8-20 (customize) |
7 | inductor furnace style | combined style joint furnace |
8 | type of drive | servo motor drive |
9 | take-up type | computer automatic control |
10 | coil weight | more than 3 tons |
11 | continuous casting machine | PLC controlled, touch screen |
12 | running capacity | 160 KW |
13 | installation capacity | 220 KVA |
14 | every ton of molten copper capacity | 320KWH |
2.Machine component
Melting-holding furnace | |||
No. | Name | Qty. | Note |
1 | melting –holding joint furnace shell | 1 set | |
2 | furnace cover | 1 set | |
3 | furnace frame | 1 pc | |
4 | inductor shell | 2 pcs | |
5 | melting channel | 2 pcs | |
6 | coil | 3 pcs | |
7 | water jacket | 3 pcs | |
8 | iron core | 3 pcs | |
9 | building furnace material | 1 set | |
10 | Ni-Cr-Ni thermocouple | 2 sets | |
11 | stand column | 4 pcs | |
12 | beam | 2 pcs | |
13 | big plate | 1 set | |
14 | furnace building floor | 1 set | |
15 | expansion ring | 1 set | |
4 strands pulling machine system | |||
No. | Name | Qty. | Note |
1 | platform of pulling machine | 1 set | |
2 | touch sc r ee n , P L C cont r o l , se r v o m o tor driving system | 1 set | |
3 | automatic serface tracking system | 1 set | |
4 | cooling water control system | 1 set | |
5 | crystallizer hanging system | 1 set | |
6 | crystallizer | 6 pcs | |
7 | protecting sleeve for crystallizer | 25 pcs | |
8 | graphite die for crystallizer | 50 pcs | |
electric system ( 6 cabinets ) | |||
No. | Name | Qty. | Note |
1 | power cabinet | 1 pc | |
2 | melting furnace voltage adjusting cabinet | 2 pcs | |
3 | holding furnace voltage adjusting cabinet | 1 pc | |
4 | capacitor cabinet | 1 pc | |
5 | operation desk | 1 pc | |
automatic rod collecting system | |||
No. | Name | Qty. | Note |
1 | automatic speed adjusting device | 1 set | |
2 |
Frequency conversion controlled automatic rod take-up machine |
2 pc s | |
3 | rail road for rod take-up machine | 2 pc s | |
4 | rod take-up car | 4 pcs | |
5 | rod take-up frame | 6 pc s |
3. Manufacturing flow
Cathode copper/Scrap Copper→melting furnace→transition house→holding furnace→casting machine (crystal molding) →casting rod→ take-up device → on sale or further producing .
Put the cathode copper into the melting furnace of Q L compounded furnace straightly. It will be melted into liquid by frequency inductor. And the liquid of copper will flood into the holding furnace automatically and smoothly pass through the transition house, and then it will be deoxidized by the charcoal covered. The liquid of copper will become casting rod quickly by the crystallizer of the casting machine in the holding furnace. Then it will be hauled by the double-withdrawal roller of the casting machine. When the casting rod is hauled off from the haul-off device, it will be led to take-up device through the idler pulley frame and take-up limited equipment .
4. Advantages
A. Control the oxygen content of copper rods to eliminate the hollow core technology . After nearly five years of continuous improvement and exploration, we has developed a unique technology, which can effectively eliminate the oxygen content of air-core and will control the 10ppm range of advanced core technology.
B. Low energy consumption, energy consumption in a single tonne 20% lower than that of similar devices . We have a great improvement in frequency furnace structure and sensors. Replaced by the W-type-furnace melting pot, the O-type-furnace, original power consumption per ton of molten copper 400 KWH drop to 350 KWH. So that saving energy of more than 20%. To the country saving valuable resources,meanwhile, to customers reducing production costs. Thus achieved remarkable social and economic benefits for the copper processing industry, energy saving and has made outstanding contributions.
C. Removable sensors, flexible maintenance, short repair time In upcast machines, the life of the hearth is generally a year and a half to two years, and the sensor is one year; our company‘s structure has been specifically designed so that the sensor can be disassembled, only the maintenance of sensors to ensure the furnace. Greatly reducing maintenance costs.
D. Computer control, servo drive system, man-machine conversation interface We developed a computer control program to control high precision, with our own intellectual property; our clients are entitled to permanent free program upgrades.
E. Automatic controlling take-up, more than 3 tons single rolling weight Winding system using frequency conversion control, linked the upward, realizes the high precision line, whose single plate rewinder weight over 3 tons, the heaviest up to four tons, which is in domestic industry leader.
F. The highest grade of the heat-resistant furnace material Our company independently research and produce the furnace material, which uses the heat resistant level-1790 degrees and alusite as main material, the heat resistance level is higher than other manufacturers of 1300-degree heat resistance level, improved the furnace service life.
1. Machinery installation layout design
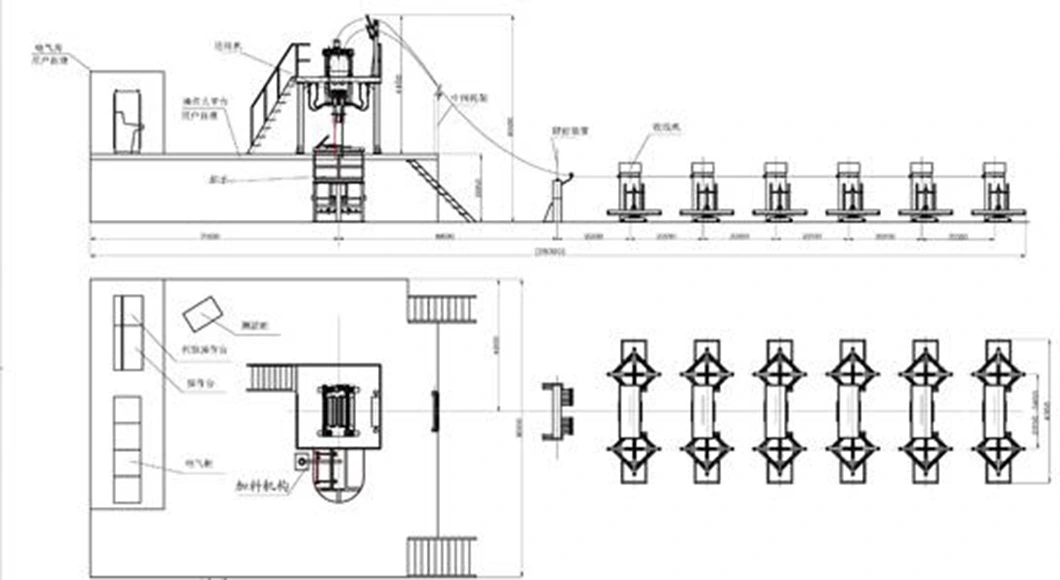
2. On-spot installation service (negotiable)
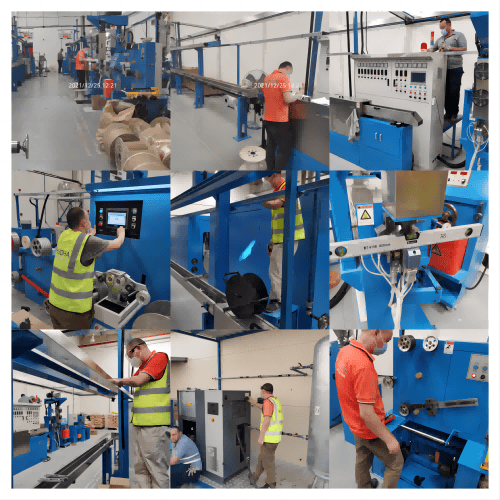
3. Whole factory layout design

4. 24-hours consulting team
