This production line is suitable for the production of scrap copper and electrolytic copper. Customers need to choose suitable furnace type according to different raw materials.
NO | Item | Technical parameter | Note |
1 | Casting Sectional Area | 2330 ㎜ ² | |
2 | Product size | Φ8mm | |
3 | CCR Capacity | 10t/h ~ 12t/h | |
4 | Coil weight | 3 ~ 5t | |
5 | Equipment dimension | 40×10×5.1m | Consider furnace, the workshop size will be suggested as 72m*18m (L*W), and the lifting height is 7m min. |
6 | Weight of Main Equipment | ~ 70T | |
7 | Power of Main Equipment | 680KW | Excludes the furnace |
8 | Rolling speed | ~ 9.5m/s(max) | |
9 | Compressed air | 6 m³/h | Pressure 0.3 ~ 0.5Mpa |
10 | Cooling water volume | 170 m³/h | Pressure 0.5 ~ 0.8MPa |
11 | Emulsion oil volume | 100 m³/h | Pressure 0.1 ~ 0.3 MPa |
12 | Lubrication oil volume | 18 m³/h | Pressure 0.1 ~ 0.3 MPa |
2.Machine component
No. | Item | Q’ty | Reference pic |
1 | Continuous casting machine | 1 | |
2 | Forward Hauling Machine and Shearer | 1 | |
3 | Casting ingot conveyer device | 1 | |
4 | Continuous Rolling Mill | 1 | |
5 | Emulsion Lubrication System for Rolling Mill | 1 | |
6 | Lubrication System for Rolling Mill Gearbox | 1 | |
7 | Oil-free enroller and drop coil take-up | 1 | |
8 | Electric control system | 1 |
3. Manufacturing flow
Cathode Shaft Melting Furnace →Holding Furnace/ScrapFlat Refining Furnace → Casting Machine→ Upward hauling,shearer, Straightening, edge shaving & brushing→Continuous RollingMill →Finishing Mill→ Rod Coolant, Cleaning, Recovery (wax coating)→ CoilingBaskets Drop Coiler/ CoilingHydraulic Take-up
1. Machinery installation layout design

2. On-spot installation service (negotiable)
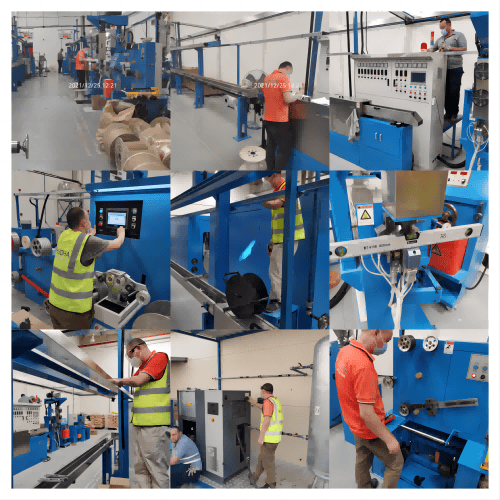
3. Whole factory layout design

4. 24-hours consulting team
